by Ishaan Goel
The first article in this series introduced two prominent types of water electrolyzers – alkaline electrolyzers (ALKEs) and polymer electrolyte membrane electrolyzers (PEMEs). Electrolyzers are devices that convert water into hydrogen and oxygen using electricity. They enable energy storage through hydrogen when combined with fuel cells, and can decarbonize hydrogen production for industry if supplied with renewable power. Subsequent articles shall focus on various characteristics of these two electrolyzer variants.
The graph above shows the investment costs ($/kW) of PEMEs and ALKEs as the technology has advanced over time. In other words, they show the initial capital cost for every 1 kW of electrolyzer capacity. The bubble size represents the total operational lifetime in hours of the technology, which is an indicator of its durability. The costs are mostly for ‘stacks’ – bundles of electrolyzers with higher capacity – rather than individual units. This article will discuss the figures for PEMEs.
Advantages of PEMEs
PEMEs have important technological advantages over ALKEs – they are compact, can tolerate higher current densities. They respond faster to changes in power supply which makes them more suitable for fluctuating power sources like solar and wind energy. However, they are yet to be as extensively commercialized, for which their cost is a major reason. As seen in the graph, PEMEs have higher average costs than ALKEs with limited reductions over recent years.
High Costs
Specialized materials and processes required within PEME stacks contribute greatly to their price. For instance, to withstand the highly acidic internal conditions, platinum and iridium are used as catalysts. Not only are the prices of these metals both expensive and volatile, but their rarity also creates bottlenecks in the expansion of PEMEs. High-priced materials themselves are about 30-40% of total stack costs, with other costs of assembly, such as coating titanium electrodes with platinum or creating the central solid electrolyte, accounting for the balance.
However, stacks are only one component of the investment costs, the other being Balance of Plant (BOP) – the cost of all auxiliary systems and components. Power prices are the most influential factor in this category, with their share of overall BOP costs exceeding 50% for larger stacks above 1 MW capacity. Other expensive systems include those for gas processing – separating, drying and pressurizing hydrogen – and for the circulation of water and cooling. The BOP itself can range from 40-70% of electrolyzer costs, depending on system size.
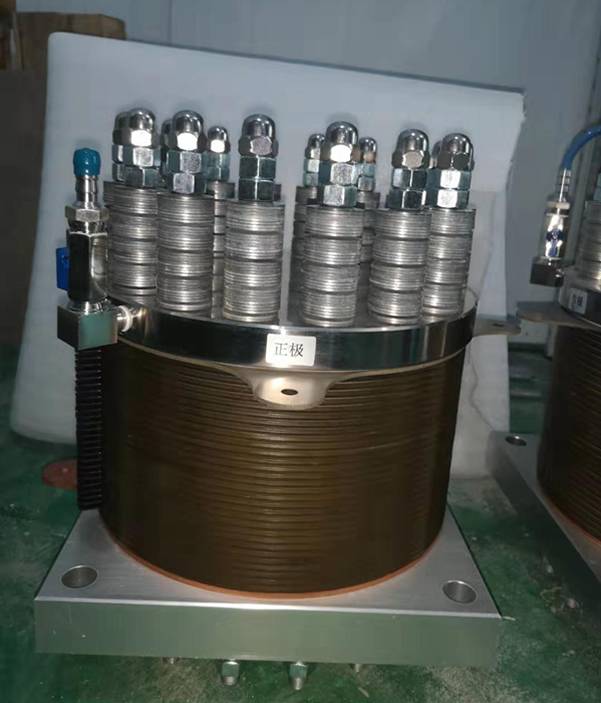
Research into PEMEs is focused on developing catalysts and other components that use less costly materials. Compounds of chemically suitable and naturally abundant metals, such as nickel, cobalt and manganese are being investigated for this purpose. Catalysts must also be made more effective to increase the capacity of stacks while keeping prices constant.
The Benefits of Scale
Beyond technical improvements, increasing the scale of production is critical to slash electrolyzer costs. This would allow suppliers of several BOP components to leverage economies of scale with higher demands. Firms would invest in shifting from manual to automated assembly processes. The lowest cost figures for PEMEs in the graph (around the $750/kW range) are projections assuming annual electrolyzer production capacities in the gigawatts. Estimates suggest that reaching 1 GW/year production of stacks with capacities between 0.2-1 MW could reduce investment costs to $300-400/kW. Such scales may not be far off – ITM Power (ITM.L, ITMPF) has already completed a factory for PEMEs with capacity ~1 GW/year, and models with capacities ~5 MW are in operation today.
With regards to durability, PEMEs lag well behind ALKEs. They exhibit operational lifetimes of about 30000-60000 hours, about half of their alkaline counterparts. This is due to various factors – unwanted reactions, formation of corrosive gases and high-temperature and high-pressure operating conditions. While PEMEs have the advantage of lower operating and maintenance costs, they will also have to be replaced more frequently due to shorter lifetimes. Resolving this issue is a technical matter, and would require catalysts effective at lower temperatures and materials more resistant to corrosion.
The multinational advisory body Hydrogen Council has estimated that hydrogen prices would have to reach about $0.5-2/kg to compete with fossil fuels. For this to feasibly occur, investment costs for electrolyzers would have to reach well under $200/kW.
PEMEs can achieve this milestone, but the journey will take time. Innovation must target the crucial challenge of eliminating the need for precious metals and boosting efficiency. Most low-cost alternatives to conventional PEMEs are either theoretical or confined to research laboratories. Firms must now fulfill their electrolyzer production commitments, so that projected cost reductions through scale are realized.
The Chicken and Egg Problem
Production capacity has to steadily increase year-on-year, but growth may end up with a chicken-and-egg problem. Firms will invest in scaling up only if there is sufficient demand in the market, but demand itself is driven by cheaper electrolyzers. As the European Union Hydrogen Strategy notes, government assistance may therefore be beneficial in the immediate term to evolve supply and demand in parallel. For instance, subsidies could be offered to firms producing and deploying PEMEs, or investments made into direct application areas like refueling stations for hydrogen automobiles. Supporting complementary products, like pipelines for hydrogen distribution or fuel cells, would induce overall sectoral growth and PEME demand.
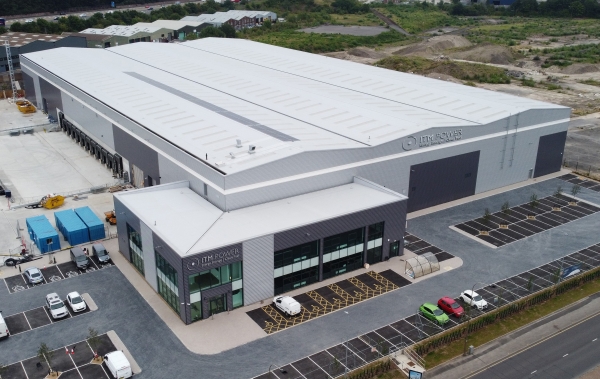
Conclusion
Given the high dependence of the cost of hydrogen produced by PEMEs on power prices, low-cost renewable electricity is imperative to achieve desired hydrogen costs. This is particularly important in industries where hydrogen is a raw material – if electrolyzers are to become the preferred means of obtaining this hydrogen, then renewable electricity costs must fall significantly. This will come about as the adoption of renewables grows, and production technologies like photovoltaic cells become cheaper. More renewables have the added benefit of potentially inducing more electrolyzer demand for supply-smoothening or energy-storage.
All the above changes will only take shape gradually. In the near future, the PEME market will be shaped by governmental action, in terms of assistance offered to producers and the broader growth trajectory of renewables and other energy-storage technologies. However, major technical breakthroughs that reduce costs may drive strong PEME growth across all their applications.
*****
Ishaan Goel is a high school senior from Mumbai, India and an incoming freshman at the University of Chicago. He likes applied mathematics and statistics, especially in relation to economics and finance. He is very interested in green energy and sustainable technologies, because of their potential and increasing relevance for the future. Ishaan’s hobbies include writing, long-distance running, playing the keyboard and coding.